How to achieve world-class manufacturing maintenance
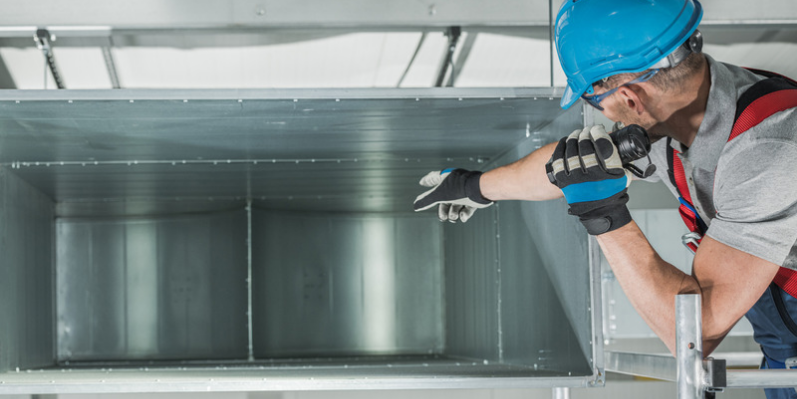
In the manufacturing sector, reactive maintenance used to be the norm, especially before the 21st century. Now, we are in the fourth industrial era.
Planned or proactive maintenance is now preferred by many organizations due to its incredible advantages, and thus it’s considered an integral component of their operations.
Emerging technologies like AI, IoT, cloud computing, robotics, and machine learning are revolutionizing maintenance in manufacturing.
These technologies enable the collection of data from several sources, including sensors on equipment, data from the production line, and maintenance plans.
Real-time analysis of this data can reveal information on how the equipment is operating, identify potential issues before they become critical, and indicate areas where maintenance can be improved.
Organizations can save costs since downtime is reduced, there is increased production, and the lifespan of equipment is extended.
This brings us to the concept of world-class manufacturing maintenance. Achieving high levels of excellence in terms of maintenance key performance indicators (KPIs) and metrics is referred to as “world-class maintenance”.
Work order completion rates, downtime, mean time between failures (MTBF), mean time to repair (MTTR), and overall equipment efficiency (OEE) are some of these KPIs. These metrics must fall within the top 5% of industry standards to be deemed “world-class”.
This implies that the organization’s maintenance output is among the best in the industry and that the organization is always exploring opportunities to enhance and streamline its maintenance operations.
Here are 3 solid strategies to achieve world-class maintenance (WCM):
Establish a detailed maintenance plan
A world’s class preventive maintenance program is built on a comprehensive maintenance plan. To establish a detailed maintenance plan, it’s crucial to conduct an assessment to see what resources and programs are already in place before starting any preventive maintenance activities, particularly if none are already in place.
There should be a detailed account of all machinery and equipment, together with clear directions and schedules for routine checks, preventive maintenance, and spare parts for replacement. Understanding significant deficiencies and opportunities for improvement can be difficult without knowledge about current activities.
Also, this strategy should be reviewed and modified often to keep it updated and relevant. A comprehensive maintenance schedule can help to eliminate downtime and extend equipment lifespan by proactively addressing potential issues before they occur.
Leverage CMMS solutions
When you manage your preventive maintenance programs manually using spreadsheets or even paper documents, there is a high chance of wasting time, dealing with redundancy, and depletion of resources.
Inventory management, equipment record keeping, and automatic scheduling and tracking of maintenance tasks are all achievable with CMMS software. This minimizes downtime, boosts efficiency, streamlines maintenance operations and elevates them to world-class maintenance.
Mobile CMMS offers additional advantages, it enables maintenance staff to view and update data remotely, which promotes speed and fosters teamwork. Mobile software solutions are now becoming so popular due to the numerous benefits they offer and their flexibility. Are you interested in these mobile solutions? Click HERE to learn more.
Ensure excellent preventive maintenance execution per industry standards
The 10% rule of preventive maintenance, which specifies that the work must be completed within a 10% variance of the time frequency of the request, is one crucial component of this strategy.
This helps to ensure that equipment is maintained in its peak working condition and scheduled maintenance is carried out.
For instance, a maintenance team has a schedule to perform cleaning and lubrication on the machines every three months. According to the 10% rule, the maintenance team is expected to accomplish these tasks between 2.7 to 3.3 months.
To simplify this, 10% of three months (90 days) is 9 days. Half of 9 is 4.5. Therefore, the tasks must be completed within 4.5 days on either side of the due date to be compliant, that is 4.5 days before or after the due date.
Conclusion
In the journey to achieve world-class manufacturing maintenance, it’s imperative to note that a reliability and maintenance policy must be regularly improved when it is established to ensure that it satisfies the changing demands of the industry and the organization.
#maintenance #industry4 #software #cmms #preventivemaintenance #worldclassmanufacturing