MTTR: Meaning, application, and the role of software in reducing it
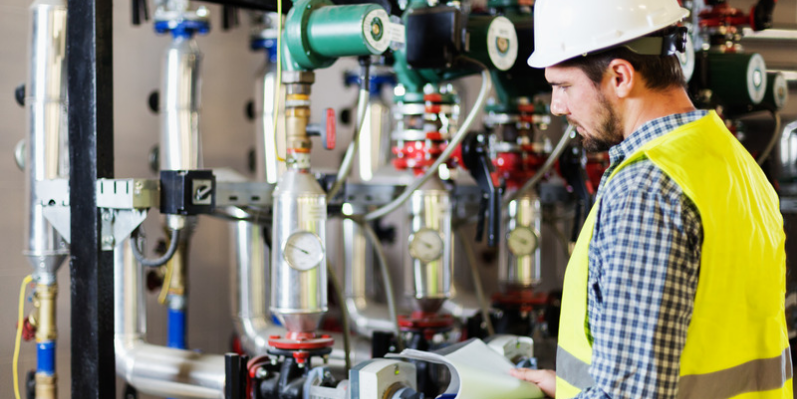
Downtime is a frequent issue in manufacturing operations, referring to any period when a machine is not in use. The primary causes of downtime include unexpected equipment failures, product changes, and labor shortages.
A 2018 report titled After The Fall: Cost, Causes and Consequences of Unplanned Downtime surveyed 450 professionals from 350 companies in the UK, U.S., France, and Germany across various industries, including manufacturing, and found that the cost of unplanned downtime was approximately $250,000 per hour, at an average of more than $2 million per downtime event.
Apart from the financial cost of downtime, unplanned downtime can affect a business’s reputation. Partnership and client connections are placed at risk owing to unanticipated delayed order delivery.
This brings us to our topic of discussion: MTTR.
In this article, we will discuss:
- The meaning and application of MTTR
- How to calculate MTTR
- How can software help in reducing MTTR?
Meaning and application of MTTR
MTTR or Mean Time To Repair is the time required to fix equipment technical or mechanical issues. It determines how fast your organization is in resolving issues in the face of unplanned downtime.
Mind you, both the repair time and any testing time are included. The timer on this metric doesn’t stop until the system is fully operational again.
This means it takes into account time to:
- Alert the technicians
- Detect the issue
- Address the issue
- Cooling down of the machinery
- Set the asset up, test it, and then launch it into production
Mean time to repair is used as a benchmark for enhancing efficiency, discovering strategies to prevent unexpected downtime, and boosting the bottom line.
An MTTR assessment can provide information on how your maintenance operation makes equipment purchases, plans out maintenance, and wraps up tasks.
The MTTR application helps your business to eliminate bottlenecks that can result to waste and financial losses.
How to calculate MTTR
By totaling the time spent on repairs over the course of a particular period and dividing it by the number of repairs, you can determine MTTR.
Assuming we’re looking at repairs over the course of a week. So, over this period, there were eight outages or downtime and systems were actively being repaired for five hours.
Five hours is 300 minutes. 300 divided by 8 is 37.5. This means the mean time to repair in this case would be 37.5 minutes.
How can software help in reducing MTTR?
Today, it’s crucial for organizations to measure and track metrics related to uptime, and downtime. Also, how promptly and efficiently teams are fixing issues is important as well.
If an equipment’s mean time to repair is already low, it means that a faulty component can be fixed quickly and effectively. If the MTTR is high, such information can help an organization with improvement initiatives.
The best way for an organization to reduce its mean time to repair is through modern tracking systems.
Monitoring, whether carried out on-site or remotely via tablets or smartphones, can offer continuous system performance reports.
An organization could determine its MTTR using this up-to-date information, enabling technicians to do preventive maintenance and make repair plans before a possible breakdown.
In recent years, a new set of technologies that enables on-call personnel to use AI and machine learning (ML) skills to avert major accidents and react to them more promptly has emerged.
This technology analyzes data produced by software systems using AI and machine learning to detect potential issues, identify the root causes, and automatically fix them.
You can use this knowledge to prepare better for troubleshooting and resolving incidents.
To learn more about this technology, CLICK HERE.
#maintenance #manufacturing #industry4 #MTTR #downtime