Everything You Need to Know About Implementing a CMMS | FAQ Guide
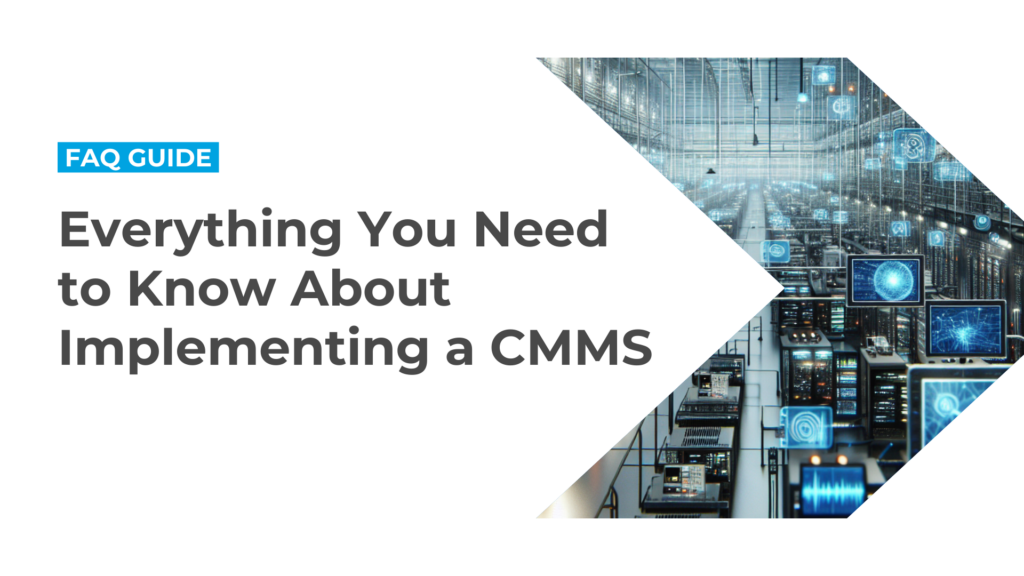
If you’re like many facility and plant managers, deciding whether or not to implement a Computerized Maintenance Management System (CMMS) can seem daunting – and oftentimes it is. But it shouldn’t be! This frequently asked questions guide answers all the common questions businesses have about implementing a CMMS to help you make an informed decision.
What is a CMMS?
A CMMS is a software system that manages maintenance operations. It tracks equipment details, maintenance histories, tasks, and suppliers. CMMS automates routine tasks like scheduling preventative maintenance, tracking work orders, and measuring key performance indicators.
How does it work?
Data about your equipment, workforce, and maintenance procedures is entered into the CMMS database. Employees then log tasks, request parts, and capture work history in the system. Managers use the CMMS to assign work, monitor project status, and analyze trends. Reports show compliance, efficiency, and costs.
Will it benefit my business?
CMMS streamlines routine maintenance for organizations of any size. By standardizing processes, you gain visibility and accountability. Reactive, costly equipment failures are reduced through improved preventative maintenance adherence and integration with ERP/MRP systems is also common.
What are the challenges?
Implementation requires gathering data, training employees on new processes and software, and adjusting to change, so choosing the right system for your needs also takes research. Gathering all required asset and maintenance data can be time-consuming to collect details on all equipment, suppliers, workforce, and procedures. Plus, staff need to learn new software and processes, which requires time and resources for training.
How much does a CMMS cost?
Costs vary depending on the solution, deployment method, and support required. Cloud-based options have lower upfront costs than on-premise software but require ongoing subscription fees. Implementation typically ranges from $10,000–$100,000. However, even small organizations see ROI within a year through efficiency and compliance improvements.
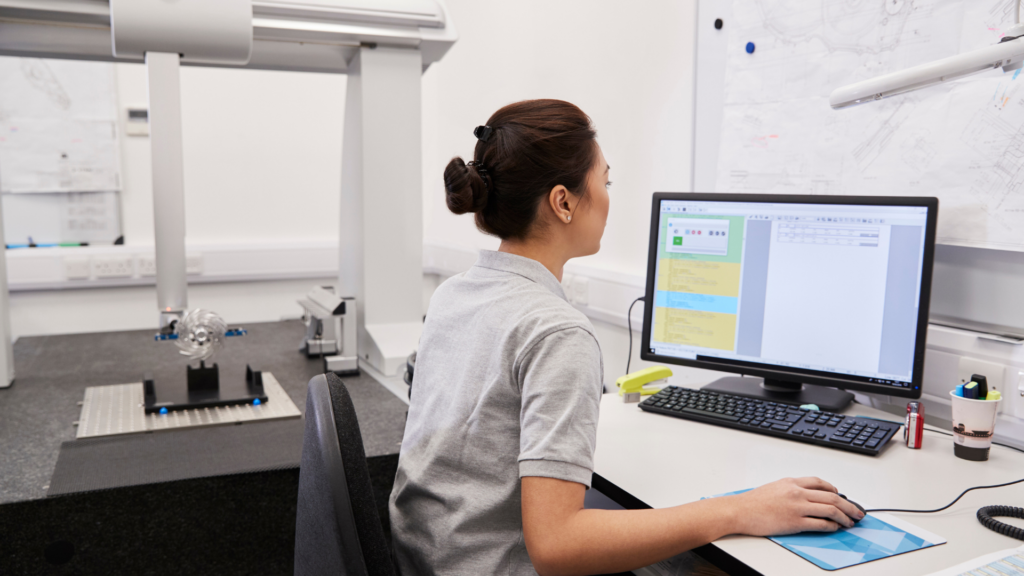
What support is included?
Leading vendors provide implementation services, training, and responsive technical assistance. Look for 24/7 support in addition to online help resources. Best-in-class vendors also offer ongoing system updates, enhancements, and roadmap consultations.
What are XMaintain’s key advantages?
When it comes to the XMaintain CMMS, there are some perks you need to know about:
· Intuitive interface
· Comprehensive work order management for preventative maintenance, corrective work, and tasks
· Flexible reporting and powerful analytics tools to gain insights into maintenance performance, budgeting needs, and compliance
· Integration with various ERP, CFW, and IoT systems
· A dedicated implementation team is available to assist with data migration, training, and go-live support
· A customizable system to fit your organization’s exact needs
Conclusion
In a nutshell, a CMMS is an amazing investment that more than pays for itself by streamlining maintenance operations. Get in touch with vendors to explore budget-friendly options that meet all your functional needs!
To learn more about how XMaintain’s CMMS can maximize equipment uptime and minimize costs for your organization, visit our home page at intec.de.
#maintenance #manufacturing #cmms #businessmanagement #efficiencygains #softwareimplementation