Maximizing Efficiency: A Guide to Maintenance Strategies and CMMS Benefits
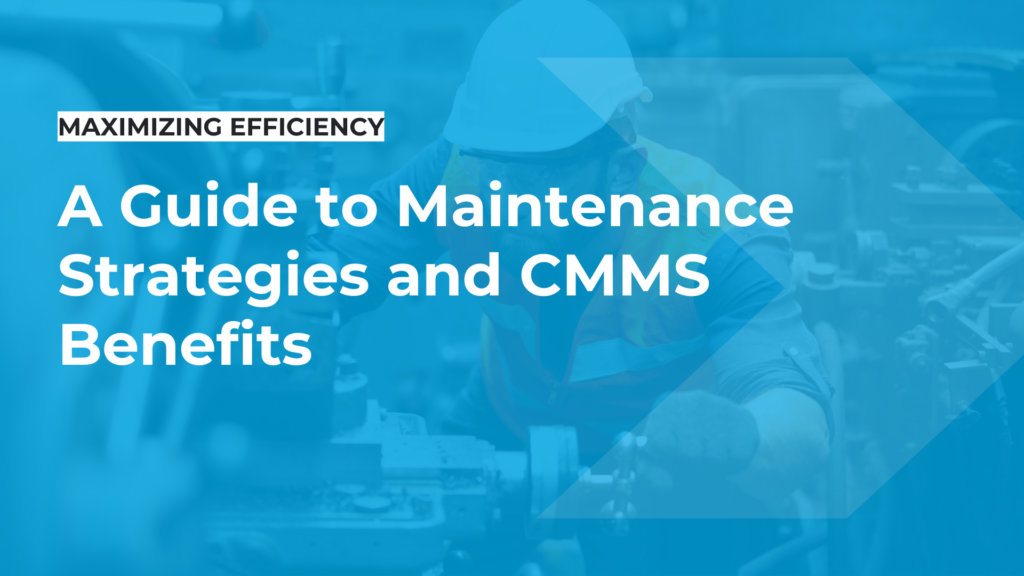
The Evolution of Maintenance Strategies
On a cool November evening in 1965, nearly 30 million people across the northeastern United States and Canada were plunged into darkness. The cause? A single overworked protective relay and the wrong maintenance strategies.
The resulting cascade of failures was pivotal. The Great New York Blackout exposed power grid vulnerabilities and prompted a reevaluation of maintenance practices.
Fast-forward to 2021, when extreme weather led to widespread power outages in Texas. Failure to winterize power infrastructure left millions enduring freezing temperatures without electricity. Despite half a century of innovation, maintenance failures have the same devastating consequences.
The lesson is universal: effective maintenance is critical to ensuring the reliability of any operation, from manufacturing lines to healthcare facilities. Unplanned downtime can disrupt production, compromise safety, and lead to significant financial losses.
But maintenance isn’t a one-size-fits-all discipline; the challenge lies in blending strategies to address unique operational needs while balancing cost and efficiency.
This guide explores four key maintenance strategies—reactive, preventive, predictive, and condition-based—and their practical applications across industries. Its insights and actionable advice will help you design an approach that ensures reliability, efficiency, and long-term success.
Reactive Maintenance: “Fix It When It Breaks”
With reactive maintenance, or the “run-to-failure” approach, repairs or replacements are only made after the equipment has broken down. It prioritizes fixing issues as they occur rather than implementing preventive measures in advance.
Reactive Maintenance Benefits
Reactive maintenance appeals to organizations with limited resources, as it requires little planning and low upfront costs. It’s suitable for operations where equipment failure is rare or has minimal impact
Reactive maintenance appeals to organizations with limited resources because it reduces initial expenses, by eliminating the need for regular inspections or servicing. This straightforward approach also requires no special tools or skilled personnel, making it simple to adopt for smaller operations.
Reactive Maintenance Disadvantages
Research reveals the drawbacks of relying only on reactive maintenance: frequent production stoppages, increased downtime costs, and reduced efficiency. It also triggers cascading failures that escalate financial and operational burdens.
Expedited shipping, overtime labor, and production delays often result in higher long-term costs. Equipment failures can lead to unplanned downtime, causing operational disruptions and revenue loss. Running machinery until failure risks severe damage and reduced equipment lifespan. Most critically, sudden breakdowns pose safety hazards, endangering workers.
When Does Reactive Maintenance Make Sense?
While not ideal for critical assets, reactive maintenance has its place in specific scenarios.
- Non-Critical Equipment. Reactive maintenance is often enough for assets whose failure won’t significantly affect operations or safety.
- Low-Cost Equipment. Replacing the asset may be more cost-effective than regular maintenance for inexpensive machinery.
- Unpredictable Failures. Assets that fail randomly make preventive maintenance less practical.
Consider a small-scale bakery using low-cost mixers for dough preparation. If a mixer fails, they may replace it instead of investing in preventive maintenance due to the low cost. This strategy is effective for a small operation but could become costly and unsustainable with larger, critical equipment.
Preventive Maintenance: Staying Ahead of the Curve
Preventive maintenance focuses on scheduled servicing, inspections, and part replacements to prevent unexpected failures. This proactive approach involves regular checks based on time intervals (e.g., monthly) or usage metrics (e.g., operational hours) instead of reacting to issues as they occur.
Preventive Maintenance Benefits
Research shows that manufacturers can achieve a 30% reduction in maintenance costs and a 25% decrease in unplanned downtime when implementing structured preventive maintenance programs.
Scheduled servicing reduces downtime to improve operations and overall productivity. Furthermore, it enhances equipment lifespan by keeping machines running at optimal performance. This approach also supports effective maintenance budgeting, avoiding the steep costs of emergency repairs. Proactively addressing potential problems reduces the risk of accidents caused by sudden equipment failures.
Preventive Maintenance Disadvantages
While highly beneficial, preventive maintenance has its challenges. It incurs higher initial costs due to regular inspections and servicing, requiring time, labor, and materials investments. Implementing this strategy is resource-intensive, demanding careful planning, skilled technicians, and robust tracking systems to ensure consistency. Additionally, the risk of over-maintenance can lead to wasted resources, especially if tasks are scheduled too frequently.
When Does Preventive Maintenance Shine?
Although it demands careful resource management, this strategy is particularly effective for:
- Critical Assets. Preventive maintenance safeguards essential equipment, avoiding significant downtime and safety risks.
- Regulated Industries. In sectors with strict compliance requirements, preventive maintenance is vital.
- Predictable Wear Patterns. Assets prone to consistent wear based on time or usage benefit significantly from this approach.
Think of a dairy processing facility where hygiene and product quality are critical. Consistent monthly checks on pasteurization equipment prevent contamination, ensure regulatory compliance, and protect its reputation. The plant avoids costly recalls and production delays by addressing minor issues early.
Predictive Maintenance: Harnessing Data for Precision
Predictive maintenance is a proactive approach that uses real-time data analytics to anticipate equipment failures. Organizations can identify and address potential issues before they arise by utilizing sensors, IoT devices, and AI algorithms, ensuring reliable and efficient equipment operation. This strategy is especially transformative in industries like manufacturing, where real-time insights can prevent costly production line disruptions.
Predictive Maintenance Benefits
Predictive maintenance maximizes uptime and minimizes waste by targeting where and when maintenance efforts are needed.
- It reduces downtime by up to 50%, with real-time insights that allow teams to resolve issues before failures occur.
- By optimizing performance, predictive actions increase asset longevity by 20-40%.
- Preemptively addressing issues leads to cost savings, eliminating emergency repairs while minimizing disruptions and unnecessary maintenance tasks.
When is Predictive Maintenance Essential?
Predictive maintenance is particularly valuable in industries where equipment failures are costly.
Manufacturing Sector. Unplanned downtime in production lines can cost up to $260,000 per hour. Predictive tools prevent disruptions by detecting issues early.
Energy Sector. Continuous monitoring of turbines and generators ensures reliability and prevents outages that could affect thousands of customers.
BMW exemplifies the power of predictive maintenance in its automotive production lines. It equips welding guns and conveyors with IoT sensors to gather real-time temperature and electrical data. Predictive algorithms analyze this data to detect anomalies early, allowing maintenance teams to address issues before they lead to breakdowns. This strategy prevents disruptions, optimizes resource use, and supports BMW’s sustainability goals by reducing waste and enhancing energy efficiency.
Condition-Based Maintenance: The Best of Both Worlds
Condition-based maintenance (CBM) is a strategy that monitors equipment in real-time to assess its condition. Unlike preventive maintenance, performed at set intervals, CBM initiates maintenance only when indicators show a potential problem.
Condition-Based Maintenance Benefits
CBM combines the proactive nature of preventive maintenance with the precision of predictive techniques. Integrating with a CMMS provides actionable insights, allowing teams to prioritize tasks effectively.
Research indicates that CBM reduces costs by up to 30% because maintenance is performed only when needed. It minimizes waste with targeted interventions that extend asset life without over-maintaining components. It also enhances equipment reliability with real-time monitoring, ensuring prompt responses and stable operations.
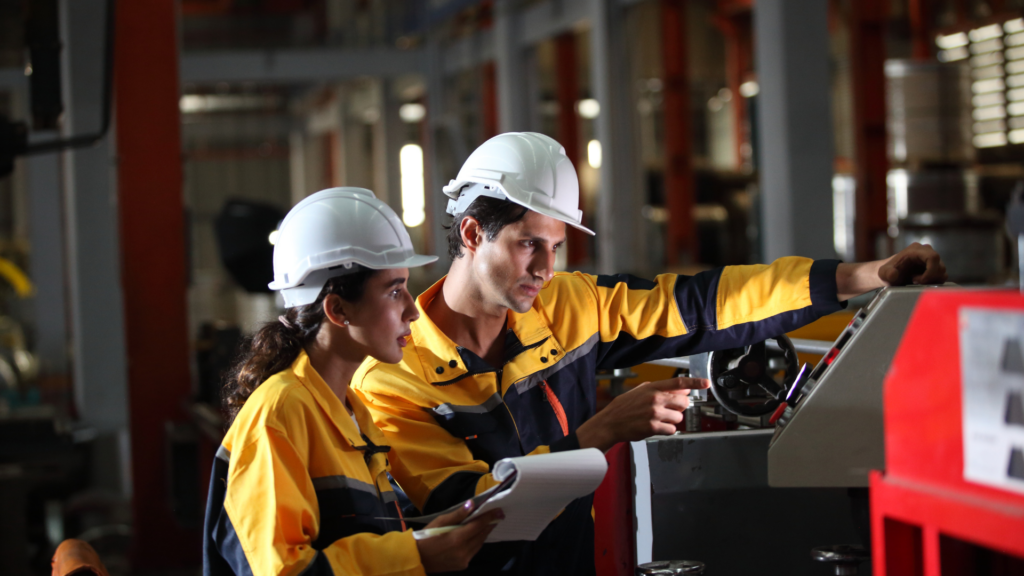
Condition-Based Maintenance Disadvantages
While CBM is highly efficient, it does have limitations. Setting up a CBM framework requires sensors, software, and training, which can add up to a high initial investment. Furthermore, data overload and ineffective analysis can lead to false alarms or overlooked anomalies.
When does Condition-Based Maintenance Excel?
CBM is especially valuable for critical or high-value assets where reliability is paramount.
- Healthcare Sector. In hospitals, CBM ensures devices like ventilators or MRI machines remain operational, where failures could have life-or-death consequences.
- High-Value Machinery. In sectors like mining or aerospace, CBM prevents costly failures and extends the lifecycle of expensive equipment.
For example, hospitals often rely on CBM to monitor critical devices like infusion pumps and ventilators. IoT sensors measure operational parameters in real-time, sending alerts when equipment deviates from normal conditions. A CMMS integrates this data, automatically scheduling maintenance and ensuring minimal disruption to patient care. This targeted approach balances cost-efficiency with reliability, making CBM an ideal solution for environments where precision and performance are non-negotiable.
Choosing the Right Strategy: A Blended Approach
Maintenance solutions aren’t universal. Each organization has unique conditions, assets, budgets, and challenges. The best approach often combines different strategies to meet specific needs and priorities.
Critical Considerations for Choosing a Maintenance Strategy
1. Asset Criticality
Identify the importance of each asset to your operations. Critical assets need proactive maintenance strategies, whereas non-critical assets can use reactive or preventive maintenance approaches.
2. Budget
Maintenance costs differ widely among strategies. Predictive and condition-based maintenance can yield long-term savings but require substantial initial investments. It’s essential to balance affordability with long-term efficiency.
3. Available Data
Organizations that effectively collect and analyze data can use predictive and condition-based strategies. In contrast, those with limited data should begin with preventive maintenance and gradually improve their capabilities.
4. Operational Challenges
Resistance to change and resource allocation are common challenges. To successfully implement new strategies, securing stakeholder support and having a clear plan for managing resources is essential.
Practical Steps for Strategy Implementation
Crafting an effective maintenance strategy requires careful evaluation and planning. Here’s a simple framework to guide your decision-making.
- Evaluate Asset Needs. Begin with a thorough assessment of your assets. Identify which equipment is critical, its failure history, and the potential impact of downtime.
- Prioritize Resources. Allocate resources strategically. Focus on advanced strategies like predictive maintenance for high-value or high-risk assets.
- Leverage CMMS. Use tools like XMaintain to integrate and execute multiple maintenance strategies seamlessly. CMMS systems provide real-time data and actionable insights, enabling you to efficiently track and adjust maintenance activities.
Research reveals that integrating CMMS into maintenance operations significantly improves decision-making and resource allocation. It enables organizations to implement blended strategies with greater precision and effectiveness by centralizing data and automating workflows.
Turning Insights into Action for Maintenance Excellence
Throughout this guide, we’ve explored four key maintenance strategies— reactive, preventive, predictive, und condition-based. Each has its benefits, from the simplicity of reactive methods to the accuracy of data-driven approaches. Successful organizations understand that a combined strategy is most effective, aligning with their specific assets, budgets, and goals.
This is where tools like XMaintain shine. A CMMS empowers teams to optimize maintenance strategies using data insights, real-time monitoring, and efficient workflows. XMaintain helps businesses minimize downtime, control costs, and enhance equipment reliability by centralizing maintenance tasks.
Take a moment to reflect on your current maintenance approach. Are your strategies aligned with your operational needs? Are you leveraging tools that maximize efficiency? Taking action today can safeguard your operations tomorrow.
Ready to elevate your maintenance strategy? Discover how XMaintain can help your team achieve a proactive, future-proof approach to asset management.