CMMS: Efficient Maintenance and its Decisive Role in the Future
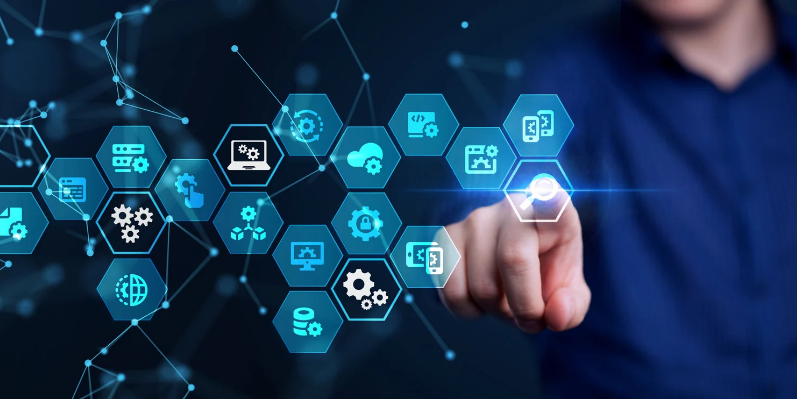
CMMS: What it is and how it can be a game changer in your maintenance strategy
The earliest CMMS systems were launched around the mid-60s, but they were only available to the biggest industrial companies with the most powerful computers.
The instruction systems created to aid in the documentation, standardization, and verification of manufacturing processes were the beginning of the evolution of CMMS.
Due to the tremendous increase in processing power and the introduction of the internet, CMMS software has greatly evolved since that time, making the capabilities available to small and medium-sized businesses worldwide.
Before CMMS, it was impractical to provide centralized, flexible monitoring and automated supervision since maintenance data were usually recorded as paperwork and scattered across spreadsheets.
Computer networks and browser connections became more common in the 2000s, extending the CMMS framework to a wide range of mobile devices, field applications, and operational locales.
The most recent CMMS technology is cloud-based and very versatile. The greater framework is supported together with quicker integration, simplified maintenance, and improved data security.
According to recent industry research, 50% of facilities currently use computerized maintenance management systems (CMMS) to handle maintenance-related tasks.
So, in this article, we’ll discuss:
- The meaning of CMMS
- The benefits of CMMS
- Three common maintenance challenges and how CMMS software can help resolve them
- Five crucial factors to consider before choosing a CMMS
- And how it will be a game changer in your maintenance strategy.
Meaning of CMMS
CMMS, or computerized maintenance management system in full form, is software that centralizes maintenance data and simplifies maintenance operations.
It helps to enhance the efficiency and mobility of physical assets, including vehicles, machines, communications, plant infrastructures, and other assets.
Manufacturing, oil and gas production, power generation, and other businesses where physical infrastructure is crucial use CMMS systems.
The structure and workflow required to manage your maintenance operation, including reactive maintenance, preventive maintenance, and predictive maintenance, are offered by CMMS software.
Additionally, a CMMS eliminates paperwork and time-consuming tasks, allowing technicians to focus more on crucial tasks and be more productive.
Benefits of CMMS
Easier record keeping
By using a CMMS for inventory management, you can quickly keep track of the cost of spare parts required for maintenance and run reports to further evaluate this data. This improves part usage and ordering.
Using a CMMS to manage maintenance and repairs streamlines record-keeping for compliance audits by storing these important documents in a single, accessible location.
Reliability
You no longer need to memorize or keep haphazard records of preventive maintenance routines when you have a CMMS.
The CMMS organizes the maintenance regularly and helps you in making sure the right resources are accessible as required and ensures that preventive maintenance takes place as scheduled.
Workflow clarity
For technicians and other roles, dashboards and infographics can be configured to track status and progress virtually in real time.
The location of an asset, what it requires, who should work on it, and when can all be quickly determined by maintenance teams.
Automation
CMMS can help you automate manual tasks like ordering parts, scheduling shifts, compiling data for audits, and other administrative responsibilities.
This helps teams concentrate on maintenance-related tasks rather than administrative ones while also saving time, reducing errors, and increasing productivity.
Health and Safety
Your health and safety team can gather data for audits, accident reports, risk analysis, and other purposes with the aid of CMMS. In a matter of seconds, they can arrange and locate certificates, rules, checklists, and audit findings.
3 Common maintenance challenges and how CMMS software can help resolve them
1. Work order management and schedule challenge
Managing and assigning work orders effectively can be a tedious task. Enhancing workflow via scheduling and work history makes the task even more demanding.
Technicians need a strategy to streamline this process to avoid costly errors while still maintaining a high level of productivity.
How CMMS can help
At INTEC digital solutions, we offer CMMS software with a feature that makes the management of work orders easy. For instance, this feature streamlines work orders from start to finish by automation.
Along with a host of other capabilities, it can generate, assign, schedule, edit, and finish work orders.
To improve workflow, multiple assets and processes can be combined on a work order, labor hours for work orders can be estimated, resources can be scheduled, and downtime monitored, among other great functionalities.
2. Lack of effective centralized management system
Using paperwork or several uncoordinated systems to manage fleets, contractors, workers, buildings, and equipment is an obsolete strategy that can affect critical operations in your organization.
To improve reporting and cost monitoring, all maintenance tasks should be managed via a single, centralized system. This helps save costs and manage risks effectively.
How CMMS can help
Simplicity is power. CMMS offers businesses the chance to simplify all important data for assets, making it easier to identify which equipment needs maintenance and where the needed spare parts are stored. Users can also generate accounting records for all repair costs and apply budget analysis capabilities to identify where their expenditures are going. Standard and customized CMMS data options assist maintenance departments to discover areas for improvement and prepare better for the future.
3. Unplanned downtime as a result of the inability to schedule effective preventive maintenance
Preventive maintenance, as we all know, helps to prevent downtime. But when it’s not scheduled properly due to certain reasons, downtime is inevitable.
How CMMS can help
CMMS helps to schedule PM for each piece of equipment as well as recording and preserve vital information such as date of purchase, repairs history, etc, linked to each asset. Application of this information makes it easy to make choices relating to equipment replacement with the history of each readily available asset. You can also monitor spare parts and inventory levels at numerous locations, which helps to reduce downtimes.
Five crucial factors to consider before choosing a CMMS
A good software solution must be customized to fit the maintenance needs of an organization to ensure the smooth running of operations and success. Here are five factors to consider while procuring CMMS software for your organization:
1. Customization and flexibility
Different organizations conduct maintenance operations using various methods. And maintenance has evolved over the years, and more development is expected in the coming years. So, when assessing maintenance software, it is crucial to think about both your short and long-term maintenance needs. Technology upgrades rapidly these days, and your CMMS software must be customized with the capability to be adjusted to meet the way your team works currently and also be adaptive to any future upgrade.
2. Scalability
The ability of software to effectively extend to match the organization’s demands is a vital element as well. If a firm is hiring more manpower to strengthen its maintenance team or is acquiring a huge quantity of equipment, more information needs to be processed and stored to facilitate these processes. A software solution should therefore be able to handle this new information development. Getting a software solution with this quality does not have to be so costly. We can offer you affordable and efficient software solutions. You can click here to learn more.
3. Ease of use
Simplicity is power. Maintenance is already a demanding and difficult operation. The last thing you want to deal with is hard-to-use maintenance software.
Therefore, you have to choose solutions that are simple to use, suit your demand, and have a great user interface. This helps to facilitate a seamless user experience and saves you the time and energy required to understand and implement software built with complex and complicated features.
4. Technical Support
Technical support is essential for ease of use. It’s therefore vital to procure from a vendor that provides technical support. It is crucial to completely grasp the facts of how help is offered and whether any payments are involved. Technical CMMS support plans often include phone and email assistance, with some vendors also giving access to other self-help tools such as videos, product documentation, and a knowledge base.
5. Mobile Access
A CMMS that can be used from smartphones enhances efficiency and decreases response times since technicians are handed work orders on the move while supervisors can review changes without being tethered to a desk. INTEC CMMS offers mobile versions accessible via smartphones and tablets, making maintenance management efficient.
Wrapping it up!
With technology, maintenance has become more efficient. Faster technician onboarding, mobile device access, increased productivity, management of work requests, and less downtime have all been made possible by work order software.
If your business has profited from employing CMMS, then CMMS’s future holds a lot more promise for you. Mobile-Ready CMMS is one of the latest and disruptive trends in CMMS software. It is a great technology to help your business scale up efficiently. With your organization becoming more complex, your staff’s time is limited, and asset management becomes more challenging, Mobile-Ready CMMS is the solution.
With this solution, employee productivity is higher since they can monitor and report job orders more quickly. Utilizing the camera on your mobile device, mobile applications let you submit pictures of work orders and scan bar codes. These smartphone applications are easy to use and offline-capable. Another trend that will be a game changer is the Internet of Things or IoT. In industry 4.0, computers can communicate with other computers without any human involvement. Smart devices can monitor themselves; they don’t need technicians to do so. Real-time data is available to maintenance managers, who can then take the appropriate actions to prevent unforeseen failures.
With better cost-saving solutions and greater profits, the future still has a lot to offer for CMMS and predictive maintenance. Click here to learn more.
#maintenance #manufacturing #industry4 #software #cmms