5 5trategies to Maximize ROI Through Effective Work Order Management
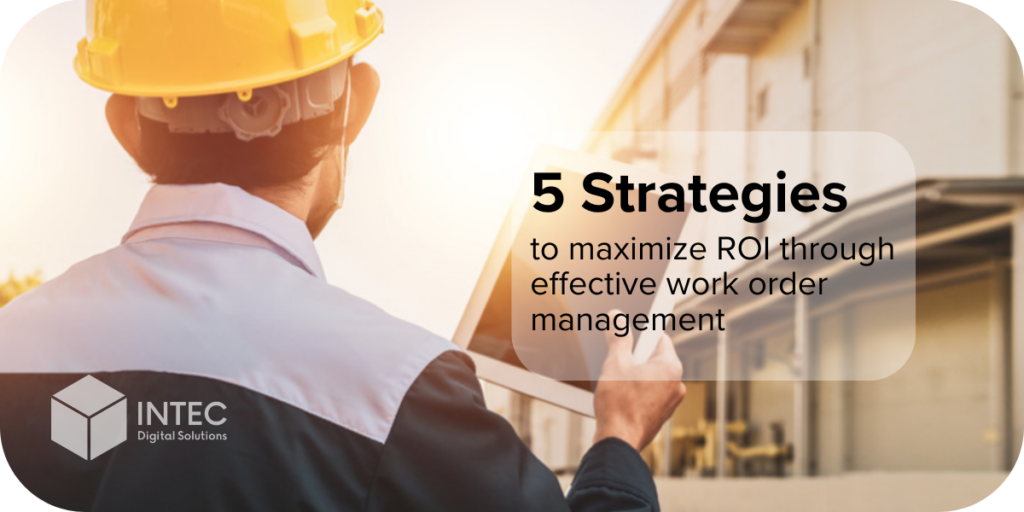
ROI (Return on Investment) is one of the most important factors for the long-term success of any business. Manufacturing companies around the world face numerous challenges, with maintenance being one of the most significant. 5 strategies to maximize ROI through effective work order management can provide a clear path to overcoming these challenges and driving productivity.
The way work orders are managed has a significant impact on efficiency and directly affects ROI. Additionally, the digital age has brought transformative innovations to the manufacturing sector, with maintenance technologies evolving rapidly since the start of the 21st century. This evolution presents an opportunity to refine processes and unlock greater ROI.
In this article, we’ll explore 5 strategies to maximize ROI through effective work order management that can make a measurable difference.
1. Implement a preventive maintenance plan
One key benefit of implementing a preventive maintenance plan is that it allows for better deployment of technicians. By having a schedule in place for regular maintenance checks, technicians can be dispatched to different facilities in a more efficient manner, reducing downtime and ensuring that any issues are addressed in a timely manner.
A well-structured preventive maintenance plan can help facilities make better use of their resources. By regularly maintaining and updating equipment, facilities can extend the life of their assets and reduce the need for costly replacements.
A preventive maintenance plan can also help save time and costs by reducing energy consumption, optimizing the usage of resources, and reducing the need for emergency repairs.
2. Link work orders to assets
Linking work orders to assets is a crucial step in maximizing ROI through effective work order management. The process involves tying maintenance and repair tasks to specific physical assets such as machinery, vehicles, or buildings.
This information helps organizations better understand the status and maintenance needs of their assets, allowing them to prioritize work and allocate resources more efficiently.
Additionally, tracking the history of work performed on assets can provide valuable insights into patterns of wear and tear, helping organizations identify potential problem areas and implement proactive maintenance strategies.
3.Create and implement templates and standard operating procedures (SOPs)
By creating checklist templates and protocols for maintenance, the guesswork for technicians is removed, and they are ensured to be compliant with operating standards for each piece of equipment.
This not only saves time and reduces errors, but also ensures that the equipment is maintained to the highest standards, leading to increased efficiency, extended equipment life, and improved safety.
4. Replace paper-based methods with software solutions
Using paper-based methods to manage maintenance work orders is a traditional practice that is becoming increasingly outdated and inefficient.
The disadvantages of these methods include poor visibility in the tracking of work orders, limited collaboration among maintenance teams, a high risk of errors, and an inability to analyze and optimize work order processes.
In contrast, spreadsheets offer a better choice as they provide a simple, low-cost way to manage work orders. However, they also come with limitations, such as a lack of automation, a lack of scalability, and the risk of errors caused by manual data entry.
Software solutions like CMMS (Computerized Maintenance Management System) are the best option for maximizing ROI through effective work order management, especially for large organizations.
CMMS solutions provide real-time visibility, collaboration, and reporting capabilities, making it easier to manage and optimize work order processes. The recent innovations brought on by these software solutions include mobile access, advanced analytics, and integration with other systems such as asset management and inventory control.
5. Adopt mobile work order management
The use of mobile devices for managing maintenance work orders is rapidly becoming a popular trend in the manufacturing sector. Our XM Mobile app allows maintenance staff to access and update work order data remotely, regardless of their location. This enables real-time updates and reduces the response time to maintenance requests.
The integration of cameras and barcode capabilities in mobile devices allows for easier identification of equipment and parts, reducing the risk of errors and improving accuracy.
The ability to capture and upload photos and videos directly from the job site provides a visual record of maintenance activities and reduces the need for manual reporting.
Moreover, the integration of barcode scanning capabilities streamlines the inventory management process and helps to reduce the risk of stock discrepancies. This also reduces the time required to complete a task and eliminates the need for manual tracking.
With these features, work order management becomes more efficient and less time-consuming, allowing maintenance staff to focus on delivering high-quality services.
Conclusion
The adoption of technology plays a crucial role in improving ROI through effective maintenance work order management. By streamlining maintenance operations, technology can reduce downtime and increase productivity, leading to a more efficient and profitable operation.
With the digitization of maintenance management, tasks such as creating work orders, tracking progress, and updating equipment information can now be accomplished quickly and accurately, reducing the likelihood of errors and improving response times.
Technology has also enabled the implementation of preventive maintenance, which helps to identify potential issues before they become major problems, reducing the risk of unplanned downtime.
This results in increased equipment availability, which translates into a higher ROI. Thus, the trend toward technology-driven maintenance management is a necessity for businesses looking to improve their ROI.
#maintenance #manufacturing #industry4 #software #CMMS #preventivemaintenance #mobile #technology #workordermanagement