Preventive Maintenance in XMaintain
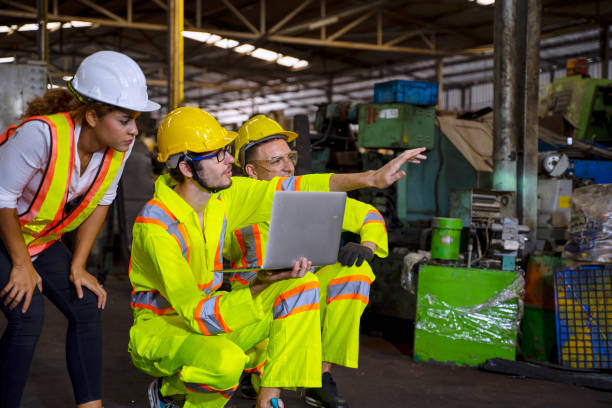
Why should you care about preventive maintenance?
The idiom, prevention is better than cure, also applies in the industrial setting. The idea of preventive maintenance is to reduce reliability risks in machinery and business operations using machine learning, operational data analytics, and predictive asset health monitoring.
In this post, we’ll discuss:
- What preventive maintenance is and how it works
- 3 reasons you should care about it
- And what to consider for a successful implementation
What is preventive maintenance and how does it work?
Preventive maintenance is the act of carrying out routine maintenance tasks to help stop unforeseen failures in the future. In simple words, it’s about fixing things before they break.
Condition-monitoring tools are used in preventive maintenance to evaluate asset performance. The implemented sensors capture a broad variety of data from the physical operations of a structure or piece of equipment, such as shocks, temperature, conductivity, etc.
Artificial intelligence or the internet of things (IoT) is a crucial component of the process, which enables many systems to collaborate in order to interpret and analyze the collected data to determine the maintenance that should be carried out.
With the reduced cost of bandwidth and storage, very large volumes of data may be collected and analyzed to provide not only a true overview of the assets in a single machine but also of the whole production network.
3 reasons you should care about preventive maintenance
- Preventive maintenance is cost-effective
According to data from the US department of energy, predictive maintenance is extremely cost-effective. A successful predictive maintenance program may provide impressive benefits, including a tenfold improvement in ROI and a reduction in maintenance expenditures of 25%–30%.
Mind you, predictive maintenance is also executed to prevent failure and damage in the future. Therefore, it’s also a kind of preventive maintenance. - It saves you the stress of equipment downtime
Unexpected equipment downtime might lead to costly process flow interruptions, equipment damage, and product waste.
Preventive maintenance can save you this stress, it can help you reduce breakdowns by 70%–75%, and an increase in uptime by 35%–45%.
- Ensures overall safety in the workplace
Everyone wants to be safe, but sometimes we don’t follow optimal safety procedures since they require more time and effort.
Nonetheless, risk control and worker safety must be top priorities in a manufacturing company. Workplace accidents, especially those related to machinery failure are not only dangerous but may also result in lawsuits with a major financial cost!
Well-executed preventive maintenance helps in the early fixing of equipment potential issues, thereby lowering the chances of catastrophic failures, and preventing injury and even death.
What should be considered for a successful implementation?
Although fixing malfunctioning equipment is a necessary component of maintenance, it can be herculean when you’re working with limited resources, getting ready for audits, compiling reports, and executing other tasks.
This is where preventive maintenance software comes in. At INTEC digital solutions, we offer software that makes it simple for maintenance teams to maintain a comprehensive and centralized record of all assets, machinery, and work.
With our software, facilities can plan, monitor, and optimize all aspects of maintenance, including work orders and inventory.
Click here to learn more.