The Ultimate Guide to Maintenance KPIs
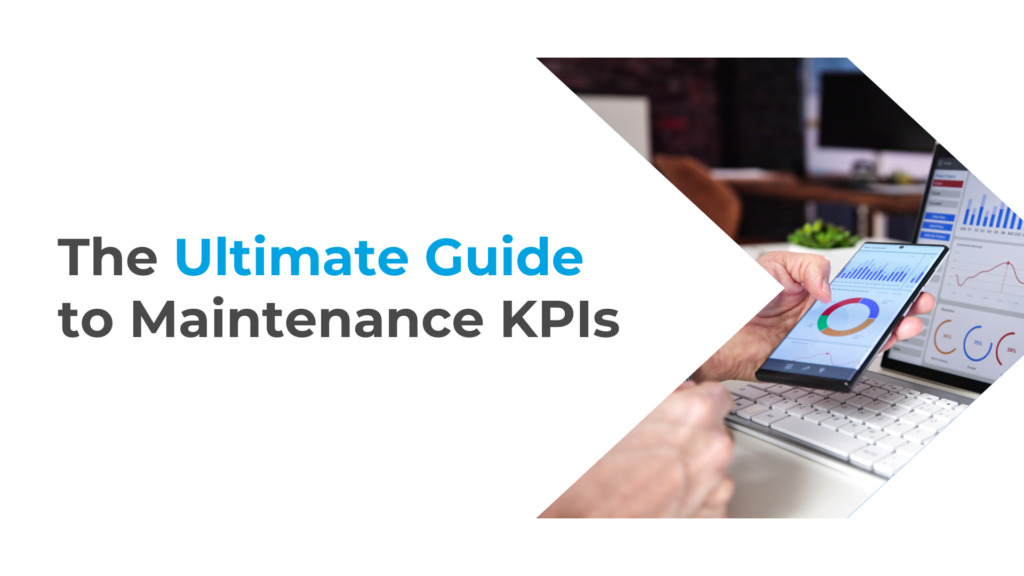
Tracking maintenance performance without clear KPIs is like navigating without a map—you might be moving forward, but are you headed in the right direction?
Without solid data, maintenance teams struggle to optimize resources, improve efficiency, and prevent costly breakdowns. Many fall into one of two traps:
- They track too many metrics, creating data overload without actionable insights.
- They track the wrong metrics, leading to reactive maintenance and rising costs.
The solution? Focus on the right KPIs. With the correct data, teams can reduce downtime, streamline workflows, and maximize asset reliability.
But which KPIs actually matter? And how can you track them efficiently?
In this guide, we’ll break down:
- The must-have maintenance KPIs every team should track
- How a CMMS helps automate and visualize KPI tracking
- How to use KPIs to drive continuous improvement
By the end of this article, you’ll have a clear roadmap for leveraging KPIs to transform your maintenance operations.
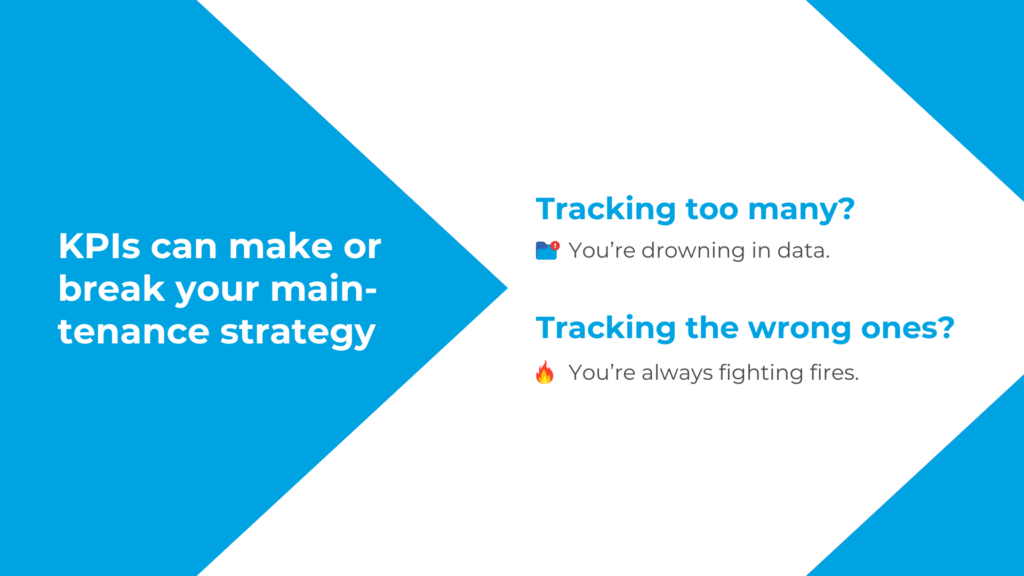
The Role of Maintenance KPIs
Every maintenance team aims to keep assets running smoothly, minimize downtime, and control costs. But how do you measure success?
That is where Maintenance Key Performance Indicators (KPIs) come in.
These metrics provide data-driven insights into your maintenance processes. They help teams identify trends, optimize performance, and make informed decisions.
The Role of Maintenance KPIs
Imagine driving without a fuel gauge, speedometer, or engine warning light. You could be moving but wouldn’t know if the vehicle is running efficiently or about to break down.
KPIs serve a similar purpose for your equipment. They offer early warning signs and real-time insights into performance.
Types of Maintenance KPIs
Maintenance KPIs generally fall into three main categories:
- Asset reliability metrics measure how often equipment fails and the duration of time it operates between breakdowns.
- Workforce efficiency metrics track how effectively maintenance teams complete tasks.
- Cost control metrics monitor maintenance expenses and help optimize budgeting.
Why KPIs Matter
Identifying problem areas before they escalate is crucial for effective maintenance management. Furthermore, optimized schedules can prevent unexpected failures, ensuring smoother operations.
Focusing on resource allocation and minimizing downtime can also significantly reduce costs, leading to a more efficient and financially sustainable approach.
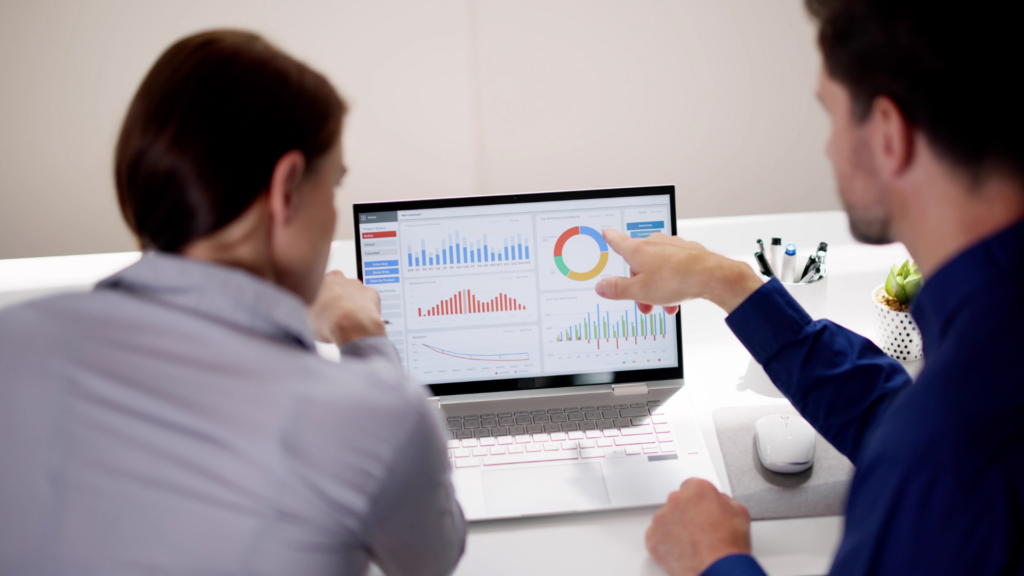
Key Maintenance KPIs You Need to Track
Not all maintenance KPIs are created equal. To maximize uptime, improve efficiency, and control costs, focus on the metrics that matter most.
Here are six essential KPIs every maintenance team should track:
1. Mean Time Between Failures (MTBF): Reliability Indicator
MTBF measures how long an asset operates before failing. A higher MTBF means more reliable equipment, leading to fewer unexpected failures and less downtime.
MTBF tracking requires consistent failure logging and precise uptime calculations. But relying on spreadsheets or written records can lead to inconsistent data and missed trends.
2. Mean Time to Repair (MTTR): Downtime Reduction
MTTR measures how quickly a team brings a failed asset back into service. A lower MTTR means faster recovery times, minimizing disruptions to operations.
MTTR tracking depends on accurate time logging from failure reporting to resolution. Paper-based logs or non-integrated systems can make pinpointing delays in the repair process challenging, though.
3. Preventive vs. Corrective Maintenance Ratio: Proactive vs. Reactive Work
This metric weighs scheduled maintenance (preventive) against emergency repairs (corrective). A higher preventive maintenance ratio means fewer breakdowns and lower repair costs.
Accurate data and swift reporting are vital to monitoring this metric. Many teams still track work orders using paper logs or spreadsheets, making balancing proactive and reactive maintenance challenging.
4. Backlog Management: Work Order Efficiency
Backlog management evaluates the number of pending work orders compared to completed ones. A growing backlog signals resource shortages or scheduling inefficiencies, leading to increased downtime.
Accurate backlog tracking requires a centralized system with real-time updates. Manual input systems like whiteboards and spreadsheets are prone to errors and delays, triggering operational bottlenecks.
5. Wrench Time: Technician Productivity
Wrench time measures the percentage of a technician’s time spent on actual maintenance work, excluding wait times for parts and paperwork. Higher wrench time translates to better efficiency and lower costs.
Accurate time tracking is crucial for spotting inefficiencies, such as delays in parts or work order approvals. Yet, many organizations rely on observational estimates or paper logs, resulting in inaccurate reports.
6. Cost of Maintenance: Budget Optimization
This metric captures the total maintenance spend, including labor, materials, and downtime costs. Understanding maintenance costs helps optimize budgets and identify cost-saving opportunities.
Getting a clear financial picture depends on precise, up-to-date data. But maintenance costs are often spread across work order logs, purchase orders, and downtime reports. This makes accurate consolidation difficult and time-consuming.
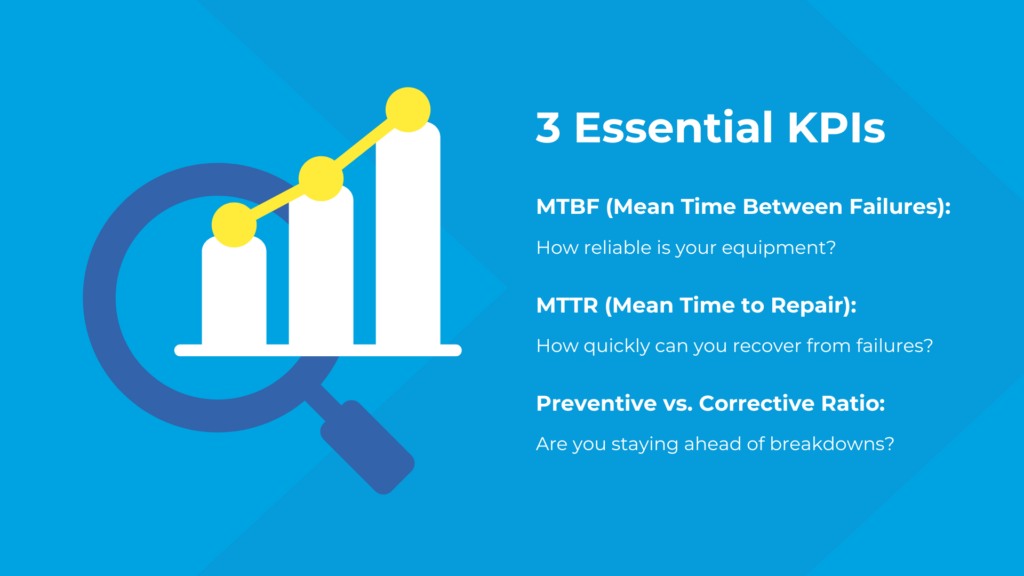
How to Set Up and Track KPIs with CMMS
Manual maintenance tracking is a slow, error-prone process. Spreadsheet entries fall behind, work orders get lost, and compiling reports can take hours if not days.
A Computerized Maintenance Management System (CMMS) removes these inefficiencies. It automates KPI tracking, centralizes data, and ensures real-time accuracy.
However, before a CMMS can deliver real value, teams must set up their KPIs correctly.
Step 1: Define Your Maintenance Goals
Before choosing KPIs, maintenance teams need to establish clear, measurable goals. Without well-defined objectives, KPI tracking becomes a numbers game with no clear direction.
A good maintenance goal is:
- Specific – Focused on a key challenge (e.g., reduce unplanned downtime by 15%).
- Measurable – Supported by data (e.g., lower average MTTR from 6 hours to 4 hours).
- Actionable – Directly tied to decisions (e.g., increase preventive maintenance tasks by 25%).
A CMMS defines benchmarks by analyzing historical data to reveal baseline performance levels. It allows teams to quickly generate reports on failure rates, repair times, and costs—giving them a realistic starting point for setting KPI targets.
Step 2: Select the Right KPIs
With well-defined goals, teams can choose the most relevant KPIs to track progress. The key is to focus on a core set of metrics that align with the maintenance strategy.
For example:
- If the goal is to improve equipment reliability, teams should track MTBF and Failure Rate.
- If the focus is on efficiency, MTTR and Wrench Time will provide insight into technician performance.
- If cost control is a priority, Maintenance Spend and Preventive vs. Corrective Ratios will highlight opportunities.
A CMMS streamlines KPI tracking by consolidating all maintenance data in one system. Teams can easily filter KPI reports by asset type, technician, or timeframe. This provides immediate insight into performance trends without the hassle of spreadsheets and separate reports.
Step 3: Automate Data Collection
One of the biggest challenges of manual KPI tracking is inconsistent and incomplete data. If failure logs aren’t updated or work orders aren’t closed properly, calculations become unreliable.
A CMMS eliminates this problem by automating data collection:
- Work orders automatically log response times and repair duration.
- IoT sensors provide real-time condition monitoring.
- Inventory tracking records usage and costs of parts flawlessly.
Every action is time-stamped and stored centrally, creating a historical record that teams can review at any time.
Step 4: Customize Your KPI Dashboard
Not every department needs to see the same KPIs. A CMMS allows teams to customize dashboards to track the data most relevant to their roles.
For example:
- Maintenance teams can link backlog management with wrench time to spot bottlenecks during work order completion.
- Finance teams can determine cost trends for each asset type, facility, or technician.
Once maintenance goals are clear and KPIs are in place, teams need a system to track performance in real-time, centralize reporting, and automate insights. A CMMS like XMaintain streamlines KPI tracking, helping teams move beyond spreadsheets and manual calculations to a more data-driven approach.
Using KPIs to Drive Continuous Improvement
A CMMS turns raw data into actionable insights to guide ongoing progress.
Step 1: Identify Trends and Bottlenecks
Without context, data means nothing. Looking at one month’s numbers doesn’t tell the whole story—tracking changes over time does.
For instance:
- If MTBF trends downward, certain assets may need more frequent preventive maintenance.
- A growing backlog may indicate a resource shortage or scheduling inefficiencies.
A CMMS makes comparing KPIs across timeframes, sites, and teams easy. Instead of manually piecing together reports, maintenance managers can spot performance declines in real-time and act before minor inefficiencies become costly disruptions.
Step 2: Optimize Maintenance Strategies with Data
Once patterns emerge, the next step is to adapt maintenance strategies based on these insights.
KPI tracking eliminates guesswork by providing concrete evidence for:
- Adjusting preventive maintenance schedules to improve uptime
- Optimizing work order flows to ensure faster responses
- Reallocating labor and inventory to improve efficiency
By leveraging historical data and real-time analytics, teams can refine their maintenance approach, improve asset reliability, and lower costs.
Step 3: Align Teams Around KPI-Driven Decision-Making
Even the best KPI tracking is useless without action to back it up. That’s why maintenance KPIs shouldn’t just be for managers.
All teams should have visibility into performance metrics, for example:
- Technicians must understand how Wrench Time and Work Order Completion Rates impact efficiency.
- Supervisors should monitor MTTR and Backlog Trends to prioritize urgent tasks.
- Executives should use Maintenance Spend and Asset Performance Data to justify budget allocations.
By making KPIs part of daily decision-making, teams can continuously refine their workflows and improve performance.
Step 4: Establish an Ongoing Review Process
KPI tracking isn’t a one-time setup. It should be a continuous feedback loop.
Teams should regularly review their top maintenance KPIs to ensure they’re making progress toward their goals. Quarterly reviews can:
- Reveal seasonal trends in asset performance
- Measure the impact of recent maintenance optimizations
- Support targets based on historical performance
With this approach, organizations can shift from reactive problem-solving to proactive optimization.
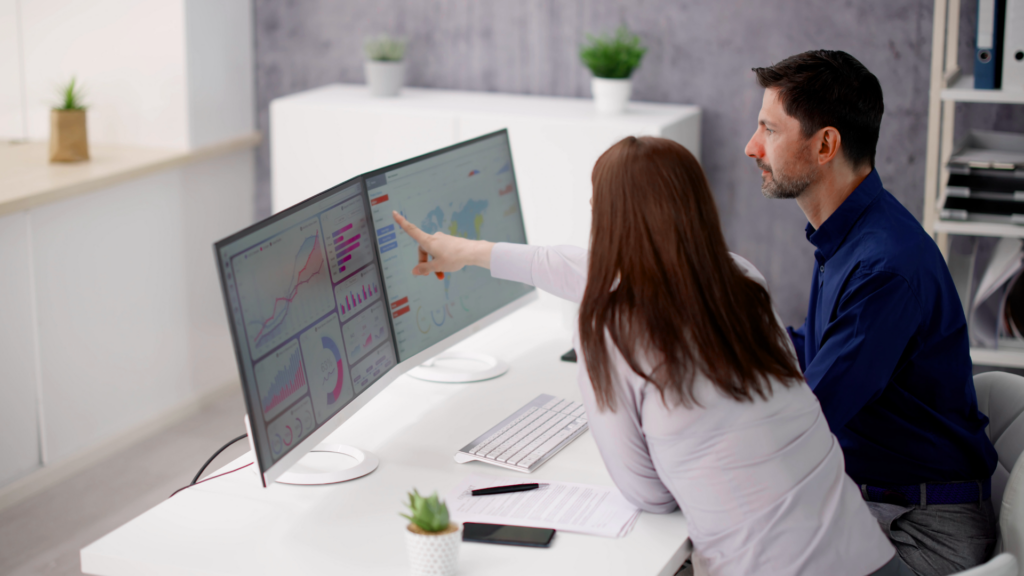
Monitoring maintenance goes beyond mere data collection. It’s about unlocking valuable
Monitoring maintenance goes beyond mere data collection. It’s about unlocking valuable insights that help minimize downtime, boost efficiency, and keep costs in check.
Similarly, a robust CMMS like XMaintain does more than track key metrics. It empowers teams to make informed decisions and implement strategic actions that drive success.
📊 Want to see KPI-driven maintenance in action? Discover how XMaintain helps teams cut downtime, improve efficiency, and optimize maintenance costs with real-time, automated tracking. Explore more here: https://intec.de/maintenance/?lang=en